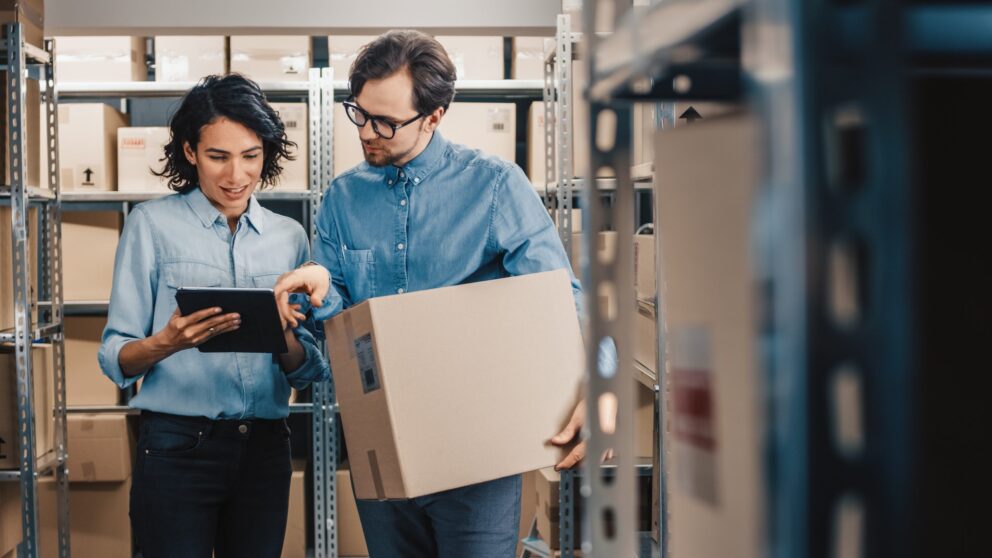
Blog
5 Ways to Simplify Inventory Management While Lowering Costs
Inventory management is one of the most critical and often overlooked functions within an organization. When it’s off, everything suffers; sales are delayed, reps can’t do their jobs, customers lose trust, and capital gets stuck in a slow-moving system. If you’re looking for ways to simplify your inventory management while also lowering operational costs, you’re not alone.
We’ve identified five customer-driven pain points that businesses are actively trying to solve, such as “how to improve inventory accuracy,” “reduce stockouts,” or “cut inventory costs”, and outlined actionable strategies that can help mitigate high carrying costs.
Whether you’re managing medical devices, field service parts, or complex service agreements, these solutions can streamline your operation and support faster growth with less waste.
1. Problem: Inventory Inaccuracies Lead to Costly Write-Offs and Delays
Solution: Real-Time Inventory Tracking with Smart Technology
Inventory errors aren’t just annoying, they’re expensive. Inaccurate inventory causes mis-picks, shipping delays, and unnecessary write-offs due to lost or expired stock. According to a report by the IHL Group, inventory distortion (stockouts and overstocks) costs retailers over $1.1 trillion annually worldwide.
The fix? Real-time tracking.
Modern inventory management solutions, most notably those powered by Bluetooth, offer visibility down to the SKU level across every inventory location. When field teams know exactly what’s in stock, where it’s located, and how long it’s been there, they make fewer mistakes and avoid costly replenishment errors.
2. Problem: Stockouts and Backorders Damage Customer Trust
Solution: Forward Stocking Locations (FSLs) for Faster Fulfillment
Stockouts not only hurt your bottom line, they can also damage your reputation. A delayed shipment might be a minor inconvenience to your team, but for your customer, it can be a serious disruption.
Enter Forward Stocking Locations (FSLs). By decentralizing your inventory through FSLs, you position products closer to the point of use, whether that’s a hospital, a service tech in the field, or a regional distribution center.
Companies that implement FSLs often see:
- Dramatically reduced shipping time
- Fewer emergency overnight shipments
- Improved fill rates and fewer backorders
If your business depends on fast response times or strict SLAs, this is a game-changer.
3. Problem: Field Reps Waste Hours Waiting for Parts
Solution: Decentralized Inventory Access to Minimize Rep Downtime
Time is money, especially when it comes to field service reps. Every hour your rep waits for parts to be delivered, or drives across town to retrieve them, is an hour not spent serving customers and ultimately not meeting SLAs.
With decentralized inventory, reps can access the items they need, exactly when they need them. This kind of setup:
- Increases field productivity
- Reduces overtime costs
- Eliminates “parts hunting” and manual tracking
Reducing rep downtime isn’t just about efficiency; it has a direct impact on customer experience and service reliability.
4. Problem: Cash Flow is Tied Up in Excess Inventory
Solution: Data-Driven Forecasting for Smarter Stock Levels
Holding too much inventory is one of the fastest ways to kill your cash flow. But cutting inventory too aggressively inevitably leads to stockouts. The balance is tricky.
That’s where demand forecasting becomes essential. A good inventory management system not only shows you what’s in stock, but ideally helps you predict what’s needed next. By analyzing usage trends, seasonal spikes, and order history, your system can recommend smarter reorder points and quantities.
The result? Less money tied up in slow-moving SKUs, fewer stockouts, and a healthier, faster cash conversion cycle.
5. Problem: Managing Inventory Manually is Time-Consuming and Risky
Solution: Automated Inventory Management Software
Manual inventory tracking with spreadsheets or pen-and-paper systems is outdated and risky. You’re relying on human input for mission-critical data, which leads to mistakes and wasted hours.
Automated inventory software provides:
- Real-time visibility across all inventory nodes
- Alerts for low stock and expirations
- Seamless integration with ERP systems
- Audit trails and compliance documentation
Beyond eliminating human error, these systems can be the backbone of a scalable operation, especially when your business model involves multiple locations or mobile teams.
Simplify Now, Save Later
The complexity of managing inventory doesn’t have to be a permanent headache. Whether you’re battling stockouts, struggling with slow cash flow, or losing time to manual processes, these five strategies give you a framework to fix what’s broken while saving money in the process.
At WA Solutions, we specialize in helping businesses like yours solve these exact problems. Our inventory management platform and nationwide network of forward stocking locations are designed to reduce rep downtime, boost inventory accuracy, and streamline the entire supply chain.
Ready to Speak to an Expert?
We’re ready to build a tech-based solution for your business.